In today's rapidly evolving technological landscape, the manufacturing industry is undergoing a profound shift propelled by digital transformation. This transformation isn't just about adopting new tools; it's a fundamental reimagining of processes, operations, and business models. Manufacturers must adopt digital strategies for survival. Success hinges on embracing transformation. Digital age demands swift adaptation. Effective strategies ensure competitiveness. Thriving requires embracing change.
Understanding the Imperatives of Digital Transformation
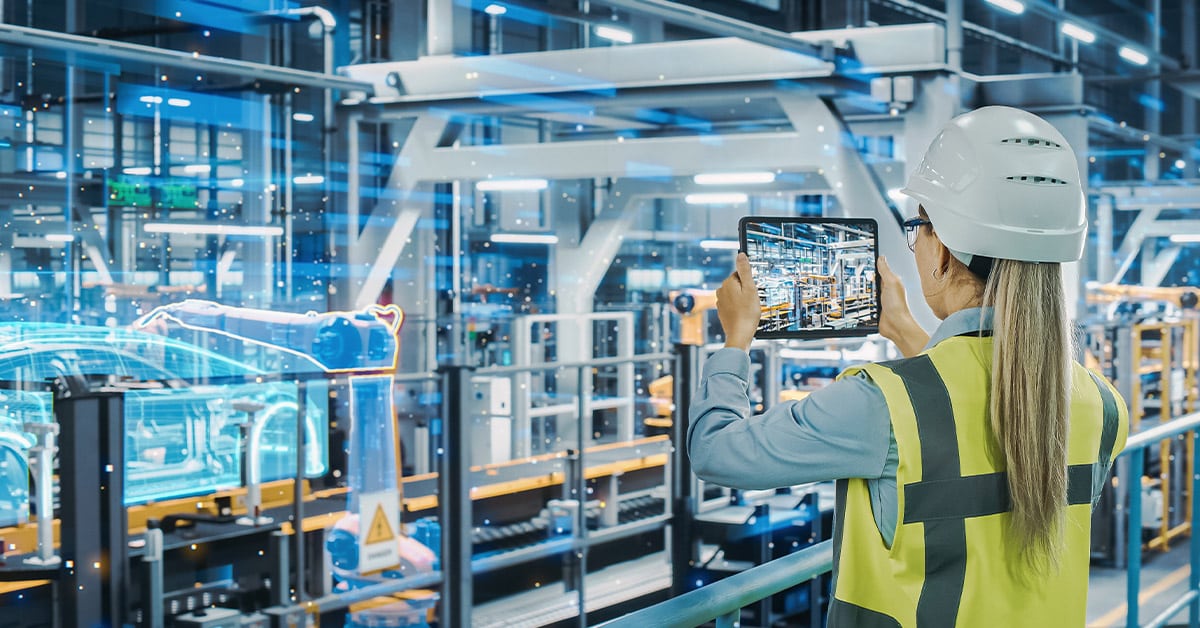
Digital transformation in manufacturing is driven by various imperatives. Improving efficiency, optimizing supply chains, meeting customer demands, and global competitiveness are crucial. Furthermore, factors such as Industry 4.0 principles, advancements in automation, and the rise of Internet of Things (IoT) technologies are compelling manufacturers to embark on transformative journeys.
Key Strategies for Digital Transformation in Manufacturing
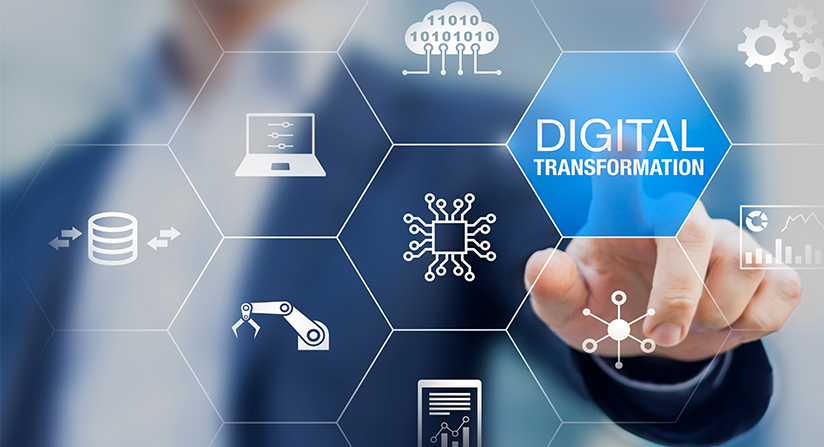
- Adoption of IoT and Connected Devices: Leveraging IoT devices allows manufacturers to collect real-time data from equipment, processes, and products. By integrating these data streams, manufacturers gain insights into production efficiency, predictive maintenance needs, and product quality. This enables proactive decision-making and optimization of manufacturing operations.
- Implementation of Advanced Analytics: Advanced analytics, including predictive analytics and machine learning algorithms, enable manufacturers to extract actionable insights from large datasets. By analyzing historical data and identifying patterns, manufacturers can forecast demand, optimize inventory management, and streamline production processes. This data-driven approach empowers manufacturers to make informed decisions and drive continuous improvement.
- Integration of Digital Twins: Digital twins—virtual replicas of physical assets or systems—offer manufacturers a powerful tool for simulating and optimizing processes. By creating digital twins of manufacturing facilities, equipment, and products, manufacturers can visualize workflows, conduct virtual testing, and optimize performance parameters. This enables manufacturers to minimize downtime, reduce operational costs, and accelerate time-to-market for new products.
- Embrace Agile and Flexible Manufacturing: In today's dynamic market environment, agility and flexibility are paramount for manufacturers. Adopting agile manufacturing practices allows manufacturers to respond swiftly to changing customer demands, market trends, and supply chain disruptions. By embracing modular production systems, collaborative robotics, and flexible manufacturing processes, manufacturers can adapt quickly to evolving requirements and seize new business opportunities.
- Focus on Cybersecurity and Data Privacy: With the increasing connectivity of manufacturing systems, cybersecurity and data privacy become critical concerns. Manufacturers must implement robust cybersecurity measures to safeguard sensitive data, protect intellectual property, and mitigate cyber threats. This includes implementing firewalls, encryption protocols, access controls, and security monitoring systems to fortify digital infrastructure and prevent cyber attacks.
Conclusion
Digital transformation holds immense potential for revolutionizing the manufacturing industry. By embracing innovative technologies and implementing effective strategies, manufacturers can enhance operational efficiency, accelerate innovation, and deliver superior products and services to customers. However, successful digital transformation requires a holistic approach, encompassing technological investments, organizational change management, and a culture of continuous learning and adaptation. By prioritizing digital transformation initiatives and leveraging the power of technology, manufacturing companies can position themselves for sustained growth and competitive advantage in the digital age.
No comments:
Post a Comment